Post by jiniya123 on Jan 3, 2024 21:46:13 GMT -6
System operators go through the warehouse locating the products that will make up a certain order. Merchandise is usually placed on carts as it is removed from the shelves. Once in the consolidation area the items are sorted into orders and distributed. With warehouse management software the person to product system can be carried out more efficiently. Because Following the softwares instructions operators travel the minimum possible distances and complete orders more quickly. Product to person The product to person method also known as goodstoperson is the most common in automated warehouses.
The operators remain at the picking stations waiting for automatic handling equipment to bring them the essential merchandise to fulfill the orders. In automatic warehouses for boxes or in a Shuttle System the products are moved with conveyors to the picking stations. There the operators receive the boxes extract the units they need from each product and the system automatically returns the remaining Graphics Design Service merchandise to the shelves. picking companies replace the manual movement and management of merchandise with machines and technologies that enable robotic order preparation from start to finish. Robots increase operational productivity because they can work without making mistakes. Automated picking systems are an ideal solution in logistics facilities with a high volume of orders or in complex environments such as refrigeration chambers.
The automatic movement of merchandise with stacker cranes conveyors or AMR robots can be complemented for example with anthropomorphic arms that manipulate items with a view to speeding up picking. Producttoperson order preparation reduces operator movements in the warehouse Producttoperson order preparation reduces operator movements in the warehouse Picking divided into sectors When planning the preparation of orders the logistics manager must decide whether to allocate a single workspace for picking or organize the operation by sectors. In this case operators are assigned a specific area to collect and prepare orders. One or more preparation areas The warehouse is separated into different sectors based on multiple criteria.
The operators remain at the picking stations waiting for automatic handling equipment to bring them the essential merchandise to fulfill the orders. In automatic warehouses for boxes or in a Shuttle System the products are moved with conveyors to the picking stations. There the operators receive the boxes extract the units they need from each product and the system automatically returns the remaining Graphics Design Service merchandise to the shelves. picking companies replace the manual movement and management of merchandise with machines and technologies that enable robotic order preparation from start to finish. Robots increase operational productivity because they can work without making mistakes. Automated picking systems are an ideal solution in logistics facilities with a high volume of orders or in complex environments such as refrigeration chambers.
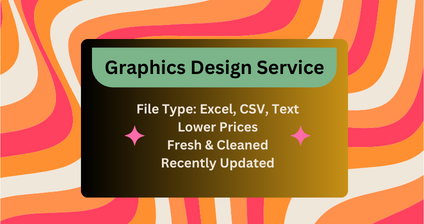
The automatic movement of merchandise with stacker cranes conveyors or AMR robots can be complemented for example with anthropomorphic arms that manipulate items with a view to speeding up picking. Producttoperson order preparation reduces operator movements in the warehouse Producttoperson order preparation reduces operator movements in the warehouse Picking divided into sectors When planning the preparation of orders the logistics manager must decide whether to allocate a single workspace for picking or organize the operation by sectors. In this case operators are assigned a specific area to collect and prepare orders. One or more preparation areas The warehouse is separated into different sectors based on multiple criteria.